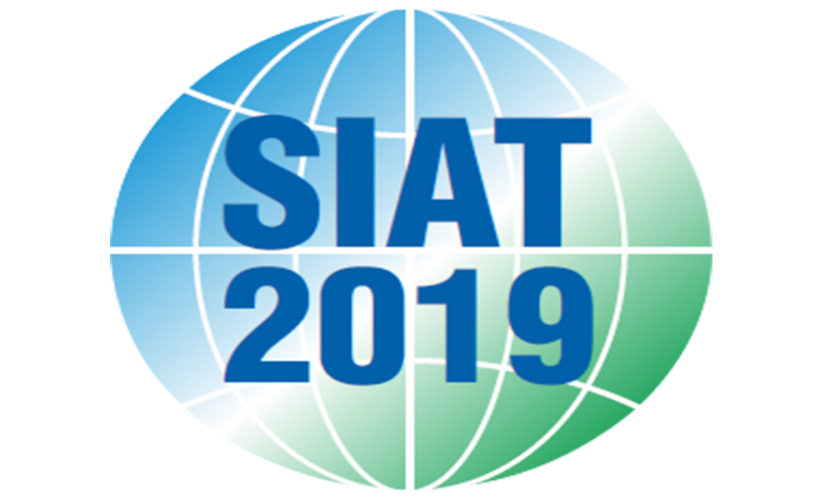
Regions around the world are faced with rising environmental challenges. Governments are trying to play their part in reducing emission and reach the committed environment goals. The Indian Government has prescribed norms such as CAFÉ (Corporate Average Fuel Economy), FAME (Faster Adoption & Manufacturing go Hybrid and Electric Vehicles) and Bharat Stage VI (BS VI) to bring India at par with the rest of the world.
Establishing such emission standards and norms will bring transformative changes in the Indian automobile industry. While, there is no doubt that electric vehicles and hybrids will continue to grow, however, there is ample room for improving the efficiency of ICEs. Schaeffler provides a range of solutions that not only improves the powertrain performance and efficiency but also increases the reliability and safety.
Schaeffler believes that globally, 30 percent of cars produced in 2030 would be using all-electric drive systems and 70 percent will have some form of ICE, either as the sole power source or in combination with an electric motor as in a hybrid. Some of the key future technologies and products that Schaeffler showcased during SIAT 2019 for emission reduction and fuel efficiency technology in India:
1. P2 hybrid module – In P2 hybridization, a powerful electric motor is installed (coaxially or even axially parallel) between the combustion engine and the transmission. In addition, an automated C0 disconnect clutch is needed so that the electric motor can also be used independently of the combustion engine for pure electric driving. the particular advantage of combining a double clutch transmission with a P2 hybrid system rather than a P2.5 hybrid system with fixed coupling of the electric motor and a sub-transmission is that the gear ratio function of the double clutch transmission can be used in all operating modes (purely electric driving, hybrid mode, and battery charging). This results in a high level of overall energy efficiency. It is also possible to drive in any situation without interrupting the tractive force, making for extremely comfortable driving.
2. UniAir – Schaeffler introduced the UniAir technology as a production-ready solution back in 2009. The same year saw its first application in the Fire MultiAir engine from Fiat. Schaeffler supplies the UniAir as a modular system comprising:
a. Electrohydraulic actuator elements
b. Control unit software module for engine management
c. Application-specific calibration data set
Schaeffler set new standards with the start of volume production of UniAir – the world’s first fully-variable electrohydraulic valve control system. The latest generation of the UniAir system not only makes it possible to reduce charge cycle losses, but also optimize combustion and achieve transient torque control via the air path.
3. Dual clutch transmission – Over the past few years, double clutch transmissions have become established as an integral part of the automatic transmission sector. They meet this sector’s high requirements for driving pleasure, comfort and efficiency. Double clutch transmissions also offer great potential for further reducing CO₂ levels as part of electrification. With important transmission components such as wet and dry double clutches and a wide range of actuators, Schaeffler has maintained its leadership position on the market in the past few years, producing more than four million double clutches per year worldwide. Schaeffler covers all vehicle segments, from compact cars to super sports cars and SUVs and develops customized solutions with the aim of improving efficiency and comfort in the power train even further.
4. Mild Hybrid P0 System – If a belt starter generator (BSG) is used in a classic auxiliary drive, this is referred to as a “PO mild hybrid.” While the focus was originally on 12-volt belt start-stop systems in the auxiliary drive, it has now shifted to PO mild hybrid systems with a 48-volt or high-voltage belt starter generator, which can be used to fulfil stricter CO₂ regulations. The central argument in favor of PO mild hybrids is their high functional scope combined with comparatively minimal integration time and effort, and low costs. This topology makes it possible to use more powerful electrical consumers, along with fast and comfortable combustion engine restart via the belt drive, and it is also capable of recuperating braking energy and feeding it back to the drive as needed, called “boosting.”
5. Electric axle drive P4 System – A significant feature of the Schaeffler electric axle is the integration of a differential with a planetary design as an alternative to the bevel gear differential. In terms of its functionality, there are no differences in comparison to the classic bevel gear differential. It provides uniform distribution of torque to the wheels and compensates differences in rotational speed during cornering. In terms of installation space requirements, the Schaeffler lightweight differential offers significant benefits compared to the classic bevel gear differential which is characterized by a compact radial design due to the lack of a drive wheel but requires significantly more space in the axial direction than the lightweight differential with the same torque capacity.